Wie nachhaltig ist Industrie 4.0?
Hand in Hand mit Kollege Roboter und selbst denkende Produktionsanlagen? Was man lange Zeit vor allem aus Science-Fiction-Filmen kannte, ist bei vielen Unternehmen schon Realität. Der vollelektrische Sportwagen Porsche Taycan entsteht in smarter Produktion, bei Wilo navigieren selbstfahrende Tische und Schaeffler baut Fabriken nach dem Schmetterlingsprinzip.
10.08.2021
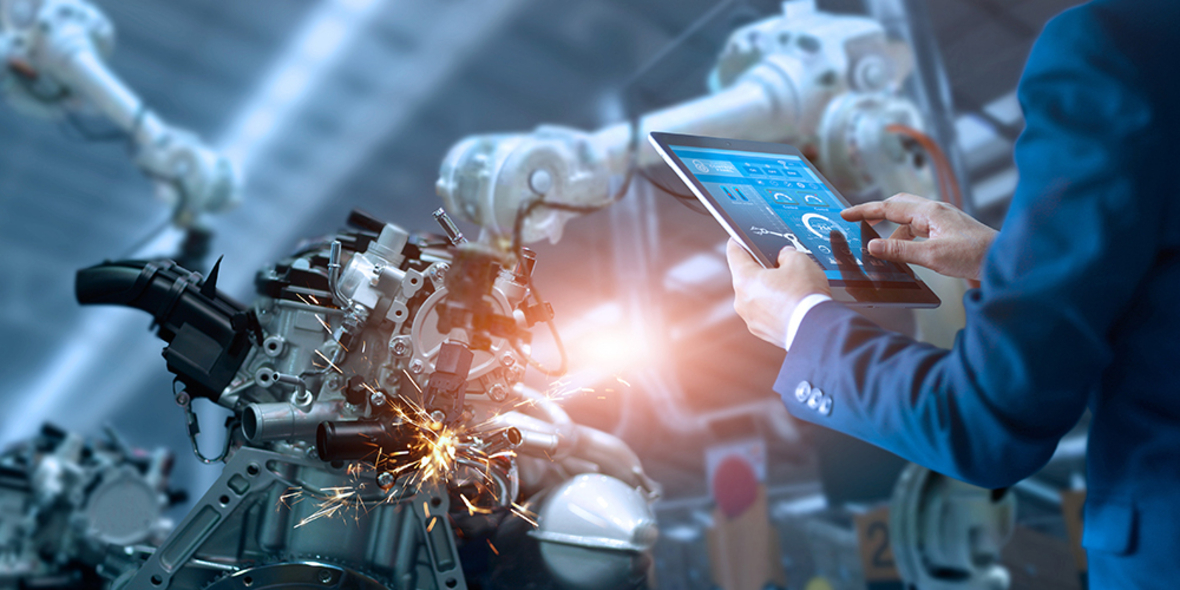
In der Geschichte der Produktion hat es nun schon einige industrielle Revolutionen gegeben: Auf die erste Revolution durch die Nutzung von Wasserkraft und der Dampfmaschine folgte durch die Erfindung des Fließbandes die zweite und mit der Einführung von Computern schließlich die dritte industrielle Revolution. Aktuell befinden wir uns dank der zunehmenden Digitalisierung und neuer Informationstechniken in der vierten Revolution – der Industrie 4.0. „Damit wird nicht nur die industrielle Entwicklung weiterer Technologien beschrieben, wie schon in den vergangenen zwei Jahrhunderten, sondern auch die geänderte Produktions- und Arbeitswelt im globalen Zeitalter“, schreibt die Informationsplattform industrie-wegweiser.de.
Die Industrie 4.0 bietet vor allem neue Chancen für die Transformation zu einer nachhaltigeren Wirtschaft. Smarte Systeme ermöglichen zum Beispiel einen effizienteren und damit sparsameren Einsatz von Ressourcen, wie die Plattform Industrie 4.0 in einem Impulspapier feststellt. „Die umfassenden Datenerfassungs- und Monitoring-Tools sorgen dafür, dass alle Materialströme und Energieprozesse gleichzeitig beobachtet und aufeinander abgestimmt werden können.“ IoT-Technologien (Internet of Things) und intelligentes Ressourcenmanagement würden außerdem dabei helfen, CO2-Emissionen einzusparen. Auch das Lifecycle-Management eines Produktes lässt sich zum Beispiel mit Hilfe eines „Sustainable Twin“ nachhaltiger gestalten. Dieser erweitert das Konzept des „Digitalen Zwillings“ (dazu später mehr) um den Aspekt der Nachhaltigkeit und enthält Informationen über den gesamten Lebenszyklus eines Produktes. Am Ende des Nutzungszyklus‘ könnten diese dann eine Entscheidungshilfe im Hinblick auf Refurbishing oder Re-Manufacturing sein. Letztlich helfe die Industrie 4.0 auch dabei, zirkuläre Wertschöpfungsnetzwerke (statt Wertschöpfungsketten) zu etablieren und so das gesamte Wirtschaftssystem als Kreislauf zu denken.
Wie genau funktioniert eine Fabrik 4.0?
Bei einer smarten Fabrik sind Maschinen und Systeme intelligent miteinander vernetzt und tauschen Informationen in Echtzeit miteinander aus, erklärt der Bundesverband der Deutschen Industrie (BDI). Die Produktionsanlagen organisieren sich selbstständig und koordinieren Abläufe und Termine ebenfalls selbst. „Dadurch wird die Produktion flexibler, dynamischer und effizienter.“ Der Informationsaustausch funktioniert dabei auch über die eigenen Werkstore hinaus. Beispielsweise könnten sich Maschinen auch mit den Systemen von Zulieferern und Kunden vernetzen. „Große Lagerhaltungen werden damit vermieden, da Lieferanten direkt nach Bedarf und jederzeit zuliefern können“, so der BDI. Auf Abweichungen oder Ausfälle könne die Smart Factory so auch schneller reagieren und nach Alternativen suchen.
Wichtiger Bestandteil der Produktion 4.0 ist außerdem der „Digitale Zwilling“. Dieser „repräsentiert ein reales Objekt in der digitalen Welt“, beschreibt das Magazin BigData-Insider das Konzept. Dabei kann es sich sowohl um materielle Objekte wie konkrete Produkte handeln als auch um immaterielle Dinge wie Dienstleistungen oder Prozesse. Im Zusammenhang mit realen Daten (zum Beispiel Umgebungsdaten oder Maschinenpositionen) ermöglicht ein Digitaler Zwilling schließlich komplexe Simulationen und Analysen – was zahlreiche Vorteile mit sich bringt: „Konzepte lassen sich im Vorfeld validieren und Prozesse oder Produkte in virtuellen Umgebungen ausgiebig testen. Die Gefahr von Fehlern oder Störungen in realen Prozessen reduziert sich. Qualitäts- und Effizienzsteigerung in der Produktion sind die Folge.“
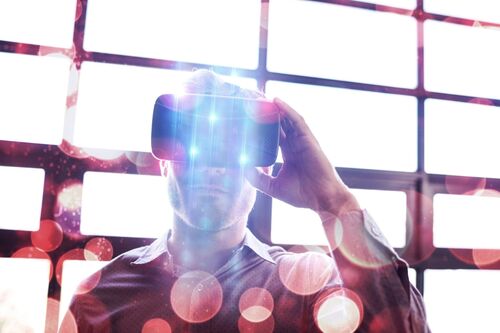
Und der Mensch? Der bleibt immer noch zentrale Figur in der Produktion, meint der BDI. Er steuere und überwache die Fertigungsabläufe und könne mit Hilfe IT-basierter Systeme wie beispielsweise einer Datenbrille „seine Sicht auf die reale Fabrik ‚virtuell‘ erweitern.“ Benötigte Informationen stünden so schnell, jederzeit und überall zur Verfügung. So unterstützen diese Assistenzsysteme „den Menschen in der Interaktion mit der Maschine, gehen auf die individuellen Möglichkeiten und Bedürfnisse der Mitarbeiter ein und bieten das Potenzial, ältere Menschen länger in das Berufsleben einzubinden.“
Herausforderungen der Produktion 4.0
Trotz der vielen Vorteile birgt die Industrie 4.0 auch einige Risiken. Die Umstellung erfordert zum Beispiel hohe Investitionen, heißt es in einem Blog-Beitrag der Haufe Akademie: „Es entstehen Kosten für Software, deren Implementierung sowie für das Personal, das mit diesen neuen Anwendungen umgehen soll. Unternehmen gehen je nach Aufwand ein hohes Risiko ein, damit der Digitale Wandel im Zuge der Industrie 4.0 erfolgreich wird.“
Auch der korrekte Datenschutz kann zum Problem werden. Durch die Vernetzung entstünden hohe Datenmengen. Jedes vernetzte Gerät könne potenziell zum Datenleck werden, über das Hacker angreifen oder andere Unternehmen Industriespionage betreiben könnten. Letztlich bestünde auch ein persönliches Datenrisiko aller an den Prozessen beteiligten Personen. Unternehmen müssen daher „nicht nur in Software selbst, sondern auch in den zuverlässigen Schutz von Clouddiensten, Apps, Anwendungen und vernetzten Maschinen investieren, und das kontinuierlich“, empfiehlt Swen Heinemann, Autor des Blog-Beitrages.
Schließlich stellt die Industrie 4.0 auch ein Risiko für das Betriebsklima dar. Zum einen könnten Mitarbeitende aus der Produktion aufgrund der Automatisierung ihren Arbeitsplatz verlieren; gleichzeitig bräuchte man neue Fachkräfte. Weiterbildungen und Qualifizierungsmaßnahmen in manchen Bereichen könnten aber für Abhilfe sorgen. „Der digitale Wandel ist in diesem Fall auch ein personeller Wandel, der am besten transparent und im Bewusstsein der Verantwortung für die Belegschaft erfolgen sollte“, so Heinemann.
Die Porsche Taycan Fabrik: smarter Fahrzeugbau auf vier Ebenen
Soweit die Theorie. Wie eine smarte Produktion in der Praxis abläuft, zeigt zum Beispiel Porsche. Der Autohersteller stampfte im Stammwerk Zuffenhausen innerhalb von vier Jahren eine Fabrik 4.0 für die Produktion des vollelektrischen Sportwagens Taycan aus dem Boden – parallel zum vollausgelasteten Produktionsbetrieb der bereits bestehenden Fabrik. Dem tatsächlichen Bau vorausgegangen war zunächst ein Digitaler Fabrik-Zwilling: „Während noch der Aushub weggefahren wurde, konnten wir mit der VR-Brille durch die neue Fabrik gehen. So konnten wir schon früh Überschneidungen der Technikebenen erkennen“, erzählt Reiner Luth, Chef der Elektrofahrzeug-Produktion bei Porsche, gegenüber der Welt. Seit Ende 2019 entstehen in smarter Produktion nun auf vier Ebenen und in verschiedenen Gebäuden zahlreiche Fahrzeuge des Porsche Taycan. Eine vollautomatische Fördertechnik transportiert die einzelnen Bauteile in die jeweiligen Ebenen, und über eine 900 Meter lange Förderbrücke gelangen die lackierten Karosserien und Antriebskomponenten schließlich ins Montagegebäude.
Statt des klassischen Fließbands kommen zudem fahrerlose Transportsysteme (FTS) zum Einsatz, die ihren Weg durch die Fabrik selbstständig finden. „Das gibt uns nicht nur neue Freiheiten im Produktionsbetrieb, sondern auch bei der Architektur des neuen Werks“, sagt Porsche-Produktionsvorstand Albrecht Reimold. Ohne starres Fließband könne man die Fertigung jederzeit modifizieren, Neues integrieren oder auch spezielle Kundenwünsche umsetzen. Um bis zu 110 Grad schwenkbare Drehgehänge erleichtern außerdem die Arbeit der Mitarbeitenden. Die stehen laut Reimhold ohnehin nach wie vor im Mittelpunkt der Produktion: „Wir automatisieren, um unsere Kollegen zu entlasten und sie bei ihrer Arbeit zu unterstützen, setzen jedoch nach wie vor auf hoch qualifizierte Fachkräfte. Denn für die anspruchsvolle Aufgabe, qualitativ hochwertige, individuelle und leistungsfähige Sportwagen auf die Räder zu stellen, ist die Kombination aus dem Einsatz modernster Technologien und dem Knowhow unserer Fachleute unverzichtbar.“
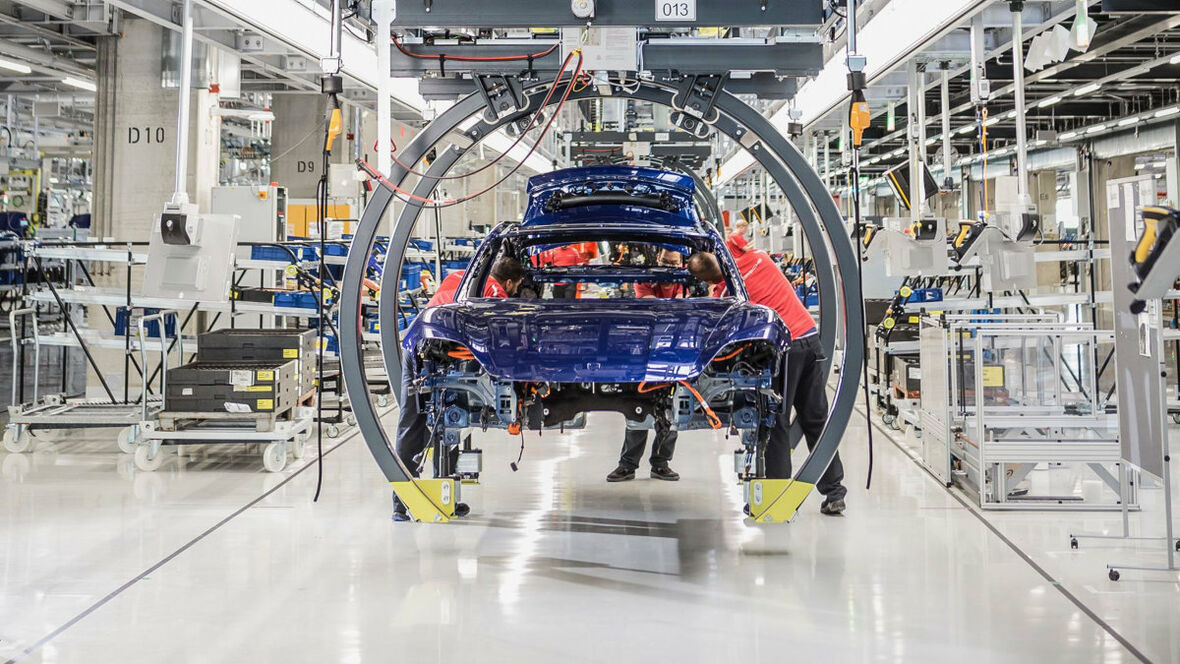
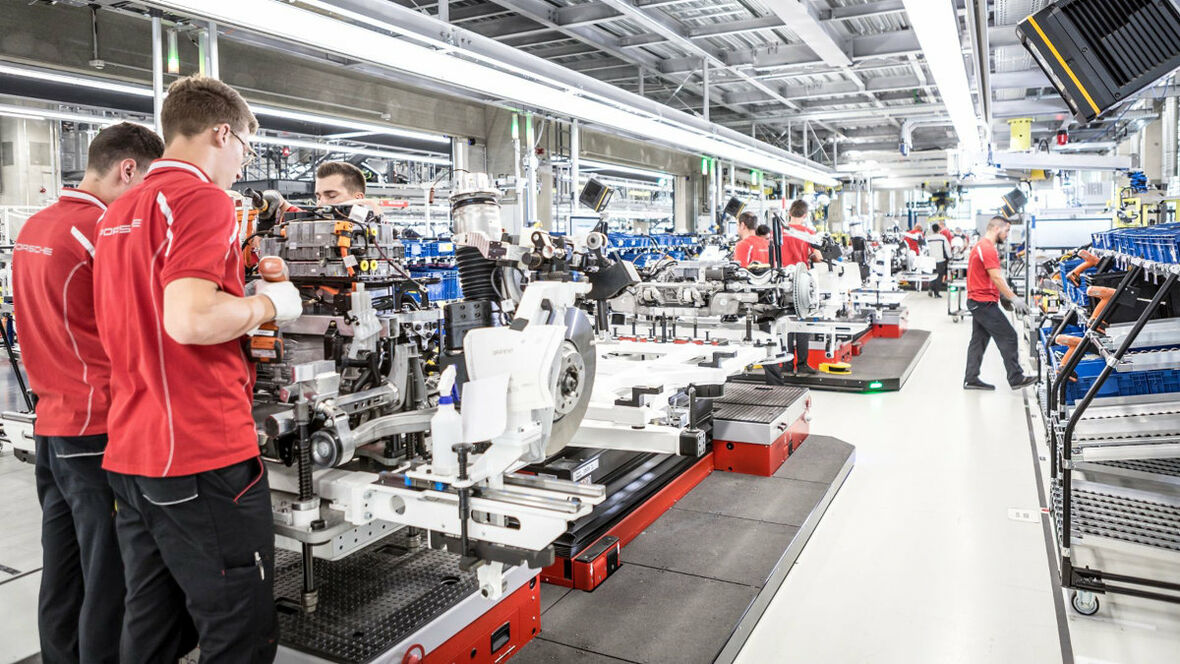
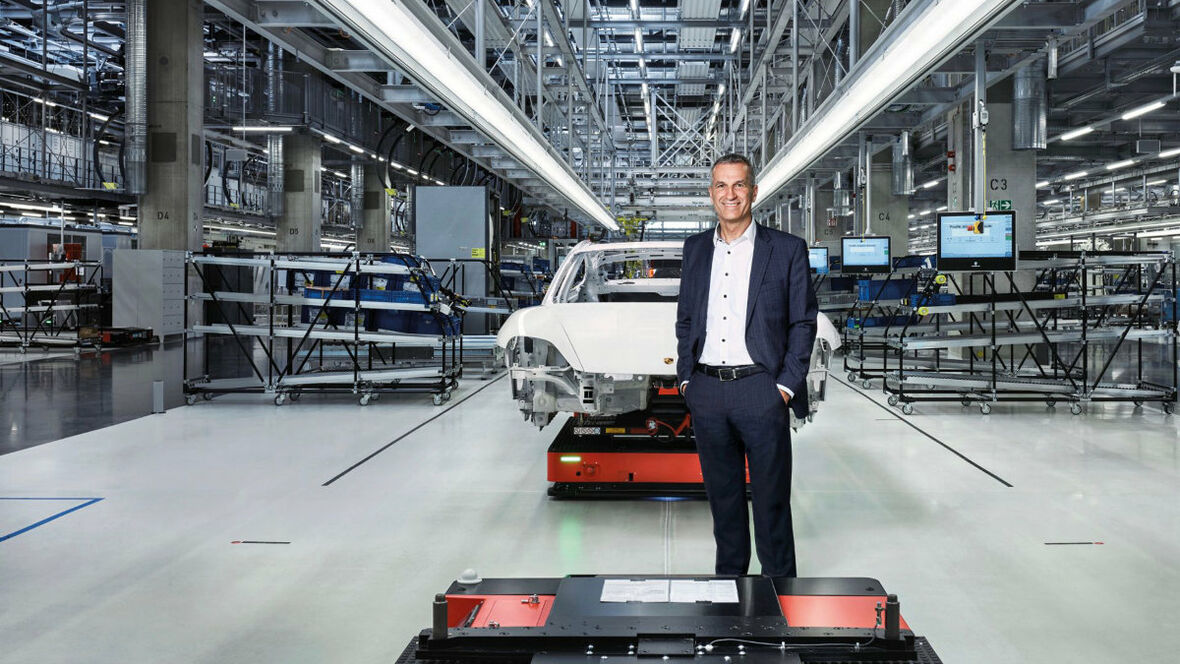
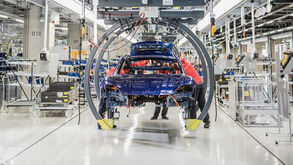
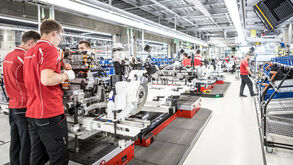
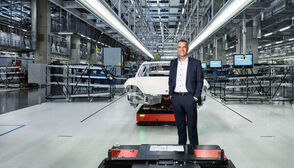
Ein schlauer Schmetterling
Mit einer Fabrik in Schmetterlingsform im chinesischen Xiantang hat auch der Industriezulieferer Schaeffler die Produktion 4.0 im Jahr 2019 in Betrieb genommen. Rund um ein Gebäude im Zentrum und ein angrenzendes Materiallager befinden sich vier weitere Hallen. Jeder Mitarbeitende – egal ob angestellt oder Führungskraft – betritt die Produktionsstätte durch das Zentralgebäude und wird durch eine Art Rückgrat in die anderen Hallen geführt. Schaeffler selbst bezeichnet diesen Komplex als „Orte der Begegnung und Kommunikation“.
Die Schmetterlings-Anordnung der Fabrik ermöglicht eine enge Kommunikation der Produktion mit allen anderen Bereichen. Durch ein standardisiertes Versorgungsraster können die Maschinen schnell und unkompliziert ans Netz gehen, und dank des modularen Aufbaus des Produktionsbereichs lassen sich neue Module für Produktionslinien und Produktportfolios leicht hinzufügen. Standardmaße sorgen außerdem dafür, dass der Bereich jederzeit an das Strom-, Wasser- und Datennetz angeschlossen werden kann. Darüber hinaus lernt die Fabrik selbstständig: Die Computer merken sich zum Beispiel, wie viel Material tatsächlich verbraucht wird, sodass passgenau nachbestellt werden kann. Fehler im Produktionsprozess werden ebenfalls schneller aufgedeckt.
Selbstfahrende Tische bei Wilo
Wilo setzt ebenfalls auf die Industrie 4.0. Herzstück der neuen Unternehmenszentrale des Herstellers von Pumpen und Pumpensystemen ist nämlich die „Factory“. Die smarte Produktionshalle besteht aus drei Hallenschiffen, die je eigene Funktionen haben. Im ersten Teil werden alle Elektronikteile für sämtliche Produktionsstätten auf der ganzen Welt gefertigt – größtenteils automatisiert. Im zweiten Teil produziert Wilo Nassläuferpumpen und im dritten Hallenschiff Trockenläuferpumpen. Selbstfahrende Tische, bepackt mit Zubehörteilen und zum Teil den benötigten Werkzeugen, bewegen sich in der Factory selbstständig zu einer der Montagestationen. Dort bauen die Mitarbeitenden die Teile in die Produkte ein. Grafisch unterstützt werden sie dabei übrigens durch Bildschirme. Nachbestellungen erfolgen automatisch, die Auslieferung wird ebenfalls digital organisiert, und auch der Maschinenpark ist komplett vernetzt und digitalisiert. Angaben von Wilo zufolge könnten rund 14.000 unterschiedliche Pumpen-Typen in der smarten Fabrik gefertigt werden.