Neue Produktionstechnologie für schwere Nutzfahrzeuge
Das EU-Klimaziel, den CO2-Ausstoß von neuen Pkw bis 2030 um 37,5 Prozent zu senken, soll bereits in fünf Jahren auch auf schwere Nutzfahrzeuge ausgedehnt werden. Forscher des Karlsruher Instituts für Technologie (KIT) erarbeiten im Projekt „KliMEA" Wege, um künftig die Produktion von Brennstoffzellenkomponenten den neuen Anforderungen anzupassen.
30.12.2020
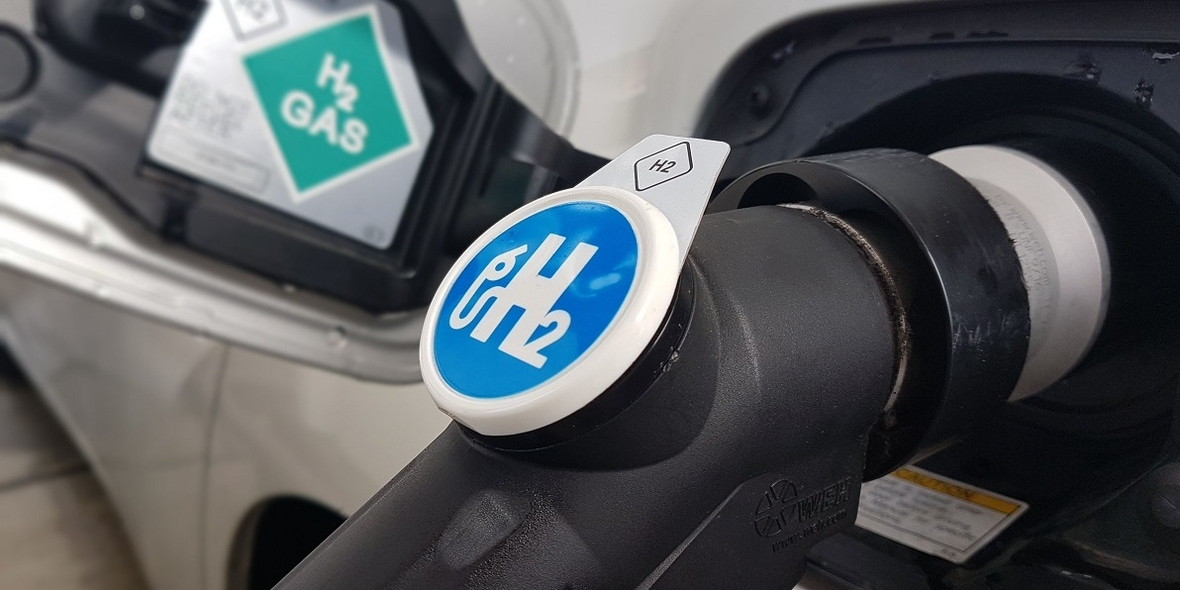
Um bis zum Jahr 2025 bei schweren Nutzfahrzeugen 15 Prozent CO2-Emissionen und bis 2030 sogar 30 Prozent einzusparen, erscheint die Brennstoffzellentechnologie vielversprechend. Konventionelle LKW-Antriebsstränge mit Dieselaggregaten sind bereits in hohem Maße optimiert und bieten hier wenig Ausbaupotenzial. Bestehende Lösungen zum batterieelektrischen Antrieb von Pkw lassen sich aber nicht direkt übertragen, da die benötigte Batterie zu schwer und die Ladezeiten zu lange wären.
„Neben dem Einsatz synthetischer Kraftstoffe sehen wir insbesondere großes Potenzial, wenn das Nutzfahrzeug über eine Brennstoffzelle durch die Nutzung von Wasserstoff mit Energie versorgt wird. Erste Fahrzeuge sind bereits verfügbar, jedoch muss die Brennstoffzellenentwicklung bei einer Einführung bis 2025 deutlich beschleunigt werden. Taktgeber für die Beschleunigung der Brennstoffzellenentwicklung ist die Produktionstechnik", so Dr. Nicole Hoffmeister-Kraut, die baden-württembergische Landesministerin für Wirtschaft, Arbeit und Wohnungsbau.
Membran in der Brennstoffzelle ist entscheidend
Bei einem Brennstoffzellenfahrzeug genügt zum Antrieb ein leichteres Brennstoffzellensystem, und der benötigte Wasserstoff lässt sich schnell nachtanken. Ein entscheidender Schritt in der Fertigung einer Brennstoffzelle besteht darin, die „Membrane Electrode Assembly" (MEA) herzustellen und zu verarbeiten. Die MEA ist ein Verbundbauteil, dessen Kernstück die Polymer-Elektrolyt-Membran (PEM) ist. Die PEM ist nur wenige Mikrometer dünn und verändert sich stark, wenn sich die Luftfeuchtigkeit ändert. Dadurch können Beschädigungen, Risse oder Ablösungen entstehen, durch die das gesamte Verbundbauteil nicht mehr nutzbar ist. Aktuell muss, um dies zu vermeiden, die gesamte Produktionsfläche klimatisiert und geregelt werden. „Ein solches System zu installieren, erfordert derzeit einen hohen Planungshorizont und verursacht hohe Kosten, sowohl in der Anschaffung als auch im Betrieb. In unserem Forschungsvorhaben ‚KliMEA‛ untersuchen wir daher die Möglichkeiten, das MEA-Verbundbauteil nur lokal in Form eines sogenannten Microenvironments zu klimatisieren. Hierbei wird die PEM an mehreren Stellen unter einer Art Käseglocke gesondert mit dem richtigen Klima an der richtigen Stelle verarbeitet", so Professor Jürgen Fleischer, Leiter des wbk Instituts für Produktionstechnik des KIT. „Mit diesem Verfahren könnten wir die MEA-Fertigung künftig stückzahlflexibel gestalten, maßgeblich beschleunigen und somit ressourcenschonender und kostengünstiger umsetzen."
Über „KliMEA": Ziele und Partner
„KliMEA" steht für „Klimaadaptive und modellgestützte Membrane-Electrode-Assembly-Fertigung". Das wbk leitet das Projekt mit zwei Fachbereichen. Als Projektpartner untersucht die Arbeitsgruppe Thin Film Technologies (TFT) des KIT vor allem das Feuchtigkeitsaufnahmeverhalten der PEM. Dieses Bauteil beeinflusst das Verhalten der MEA wesentlich. Es wird länger oder kürzer, wenn sich die Luftfeuchtigkeit verändert. Ein Team des wbk untersucht darauf aufbauend in Simulationen genauer, wie sich die Veränderungen der PEM auf die MEA auswirken, um so das nötige Prozesswissen zu erlangen. Mittels eines „digitalen Zwillings", also einer betriebsbegleitenden Simulation, die sehr realitätsnah und ausreichend detailliert das System digital widerspiegelt, untersucht das zweite Forschungsteam des wbk die Verknüpfung mit der realen Anlage und leitet geeignete Messstrategien ab. Die erhobenen Daten sind entscheidend für die Qualitätssicherung und zugleich für die Rückverfolgbarkeit (Traceability). Auf dieser Basis lässt sich entscheiden, ob hinsichtlich einer bestimmten Baugruppe ein Risiko besteht und Gegenmaßnahmen ergriffen werden müssen.
Als assoziierter Projektpartner bringt die Daimler Truck Fuel Cell GmbH ihr Expertenwissen zur industriellen MEA-Fertigung ein. Die e-mobil BW GmbH unterstützt das Projekt mit ihrer Kompetenz aus dem langjährigen Management des Clusters Brennstoffzelle Baden-Württemberg. Im Rahmen des Strategiedialogs Automobilwirtschaft Baden-Württemberg fördert das Ministerium für Wirtschaft, Arbeit und Wohnungsbau das Forschungsvorhaben bis Ende 2021 mit rund einer Million Euro.